In the high-speed product development environment, rapid-prototyping services are considered the foundation for the automotive, aerospace, and medical device industries. While the name may imply just speed, the main object of rapid prototyping is not just that, but a holistic process that guarantees that a design is ready for the shift from concept to production. This entails a functional validation, structural tests, and machining feasibility assessment —three critical pillars that determine whether a prototype can withstand real-world conditions and meet manufacturing requirements.
Functional validation is when a prototype does its intended task; it may be a part of an engine, say a gear, or it can be a dashboard part of a car. Structural testing determines the tolerance of the parts to stresses, vibrations, and environmental effects. In the meantime, machining feasibility assessment ensures whether the design can be mass-produced without quality hampering or the cost skyrocketing.
These needs challenge a key issue of prototyping, that is, combining speed, precision, and reliability. While emerging technologies like 3D printing and additive manufacturing continue to gain attention, CNC machining services remains the cornerstone of high-precision rapid prototyping.
Limitations of 3D Printing and the Rise of CNC Prototyping
The rise of additive manufacturing, especially 3D printing, has undeniably transformed rapid prototyping services. It promises design freedom, short turnaround times, and less waste of material in the case of complex geometries. However, the above merits 3D printing are subject to limitations in situations that require high precision, durability, and surface quality.
First, material strength is still the key deficiency of most 3D printing technologies. Many additive manufacturing processes use polymer-based materials or metal powders. These materials or metal powders do not produce the same mechanical properties achieved with billet metals or engineering-grade plastics used in CNC machining services. Members that are tested for structural stress or functional loading often fail when they are made using traditional 3D printing material.
Secondly, dimensional accuracy and tolerances attainable by 3D printing tend to fall short of those of CNC machining. Layer-based construction introduces anisotropy and can cause warping, shrinkage, and/or irregularity – all of which impair tight tolerances. Surface finish remains a challenge; printed parts often need some post-processing to make them smooth, which costs time and complexity.
But CNC machined prototypes can be made from solid metal or engineering-grade plastic blocks and have similar mechanical properties, higher durability, as well as dimensional consistency. Such attributes are important for prototypes that are going to be used for functional testing, precision assemblies, or regulatory validation.
CNC Machining in Rapid Prototyping Services
Even though rapid prototyping services provide a range of technologies, CNC machining services can be the preferred technology choice under certain engineering settings. There are three dimensions to help determine its necessity: material needs, dimensional precision, and structural intricacy.
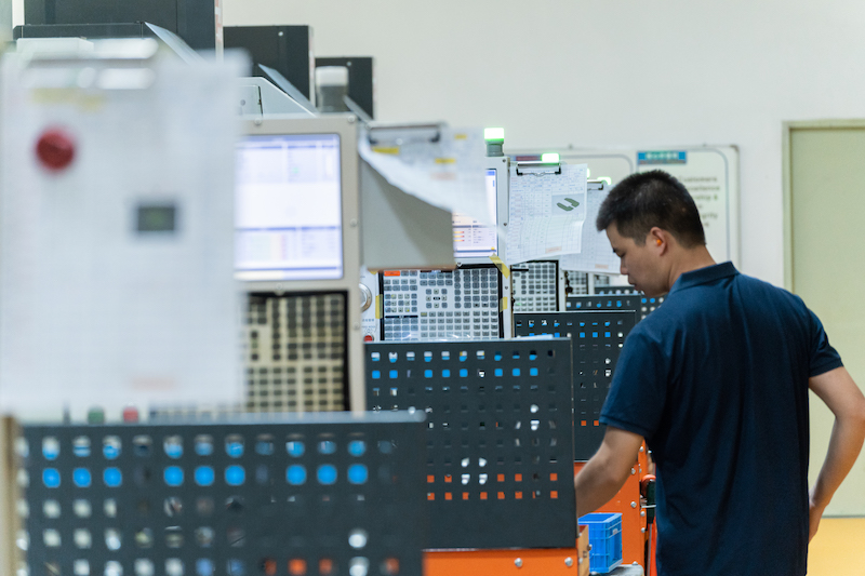
Material Requirements
When prototype components must be made from production-grade metals such as aluminum, titanium, or stainless steel, or from high-performance plastics such as PEEK or Delrin, then CNC machining is often the only practical approach. Unlike 3D printing, which has both material variety and material authenticity limitations, CNC machining services allow for prototyping using material identical to final production components. This material fidelity is essential for situations where prototype parts are put through real-world mechanical/thermal/chemical testing.
Dimensional Accuracy
Tolerances can be as tight as ±0.01 mm in such industries as aerospace, medical devices, and automotive engineering, among many others. CNC machining services can continually reproduce such tolerances, and it is essential for certifying fit, alignment, and assembly. Furthermore, 3D printing is free from typical problems of layer shifting or warping, and therefore geometrical integrity is assured even in the case of thin-walled or complex parts.
Structural Complexity
Although 3D printing is suitable for a range of organic shapes and internal cavities, CNC machining services are better when an external complex geometry, drilled precision openings, and flat mating surfaces are required. Non-machined prototypes that interface with existing parts, such as mechanical housings, engine parts, and fixtures, need the rigidity and repeatability of CNC machining for assembly testing.
Streamlining the Prototyping-to-Production Transition
CNC prototyping helps the engineers identify design flaws soon through very precise physical models. Prior to making the costly tooling investment, parts machined to production-grade tolerances will expose any misalignments, interference issues, or manufacturability issues. Such real-world feedback quickens the design iterations and reduces the possibility of late-stage design modification.
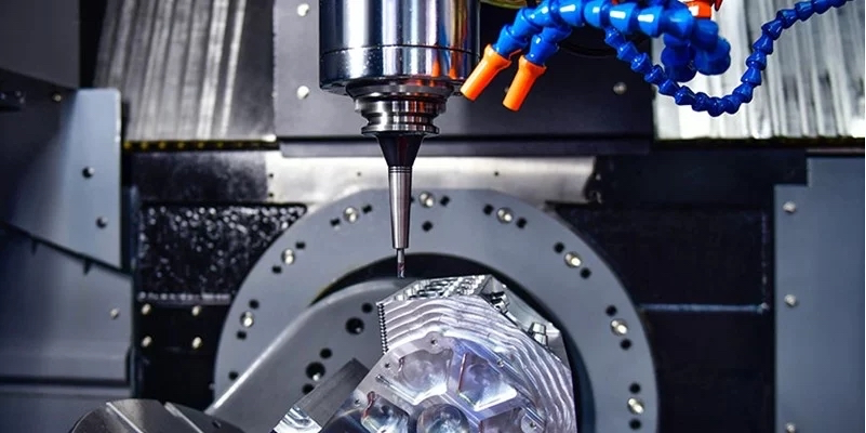
Besides, since the same CNC equipment and processes can be applied to the makings of prototypes and for low-volume production runs, switching over to initial production batches becomes unobstructed. Customer gains consist of equal prototyping and final product part quality, thereby lessening validation delays.
For example, in automotive applications, CNC machining services enable manufacturers to prototype a working metal bracket or an engine part subjected to durability tests. Once validated, the same machining paths could be scaled for production for limited runs, while tooling for mass production came online. Such continuity maximizes time-to-market and production reliability.
Conclusion
Despite the rise of new fabrication technologies, CNC machining continues to play an irreplaceable role in rapid prototyping—especially when precision, repeatability, and material versatility are paramount. Its ability to bridge the gap between concept and production with speed and accuracy ensures that engineers and product developers can bring reliable prototypes to life. As the demands for quality and efficiency grow, CNC machining remains not just relevant, but essential to high-precision prototyping in today’s competitive landscape.